To those who own a business particularly those engaged in the movement of stocks or equipment, having a storage trailer is a must. Storage containers are specifically designed to offer protection from the elements and theft to valuable stock and other items.
Nevertheless, with such varieties of storage containers, choosing the most suitable type or size can sometimes be a herculean task. In this regard, you should pay attention to several factors such as storage space, accessibility, environmental conditions, the level of protection, and cost.
This will assist you in making the right decision on the most appropriate storage unit to securely store your business physical assets. So, continue reading before you look for ground level storage containers.
Type Of Goods Storing
First, decide what types of products you will be transporting in your trailer. For instance, is it necessary to store musical instruments, perishable goods, toxic materials, or massive machinery?
The contents that will be stored will define the specific features like storage space, ventilation, or types of shelves. It needs to have the right qualities that would enable the storage trailer to handle your specific goods adequately.
Storing improper material in a trailer that is not suitable for such might cause damage, harm or even compliance problems. Before you go out to look for a trailer to hire or purchase, you must consider what you will be storing carefully because this is the most vital factor in selecting the right storage trailer.
Required Storage Capacity
To choose the right trailer, you need to consider the volume and weight of items that are expected to be stored. If one underestimates the capacity, it results in containers that are overcrowded and messy, whereas overestimating is costly since you will end up paying for space that is not needed.
Inventory of the current stock and take an approximate of the amount that may be required in the near future. Estimate the dimension of all items and determine the total volume in terms of cubic feet and total weight to be stored.
It is suggested that the extra 20% space be provided for the future growth of the inventory. Also consider pallet/shelf footprints, as there must be a workspace for pallet jacks, pallet guns, etc. around the stored goods.
Use Frequency And Ease
Consider how frequently stored goods will need to be retrieved and whether convenient access is essential. For instance, does a worker need to get to certain inventory several times daily, for example, to load or unload, where a trailer will have wide doors and no spaces that are difficult to access?
Or will goods be stored for a long time with the need for access very rare? Access enhanced designs feature roll up doors, multiple access points, few walls of shelving within the unit, and adequate space for forklifts or pallet jacks.
Selecting portable concession stand with size and shelving that is appropriate to the frequency of the required access and goods Enables efficient warehouse organization.
Climate And Humidity Control
It varies depending on the storage containers. When transporting products that are sensitive to temperature such as foods, chemicals, and pharmaceuticals, opt for insulated containers with HVAC systems to control the climate.
Choose such features as thermostatic controls and air conditioning/ heating options in order to set temperature preferences throughout different seasons.
As long as there is a passive form of ventilation to avoid condensation, it should be fine. Ensure that climate specifications for safe product storage correspond with suitable trailer environmental settings. This helps stop inventory degradation from wrong conditions.
Conclusion
The ways and methods used in storing inventories have a direct relation to the efficiency of any business enterprise as well as its revenues. Selecting the wrong storage containers indifferent to the items stored, fosters improper stocking, product damaging, and at times even dangerous conditions resulting from careless handling.
By taking into account the stored goods types, required storage volume, access frequency, climate requirements, security measures, and cost constraints one can choose the most suitable containers meeting organizational needs.
This cuts costs from expenditure on unutilized space or unneeded amenities in a building. Thorough assessment of storage requirements provides cost-effective, relevant containers enhancing warehouse organization and inventory accuracy.
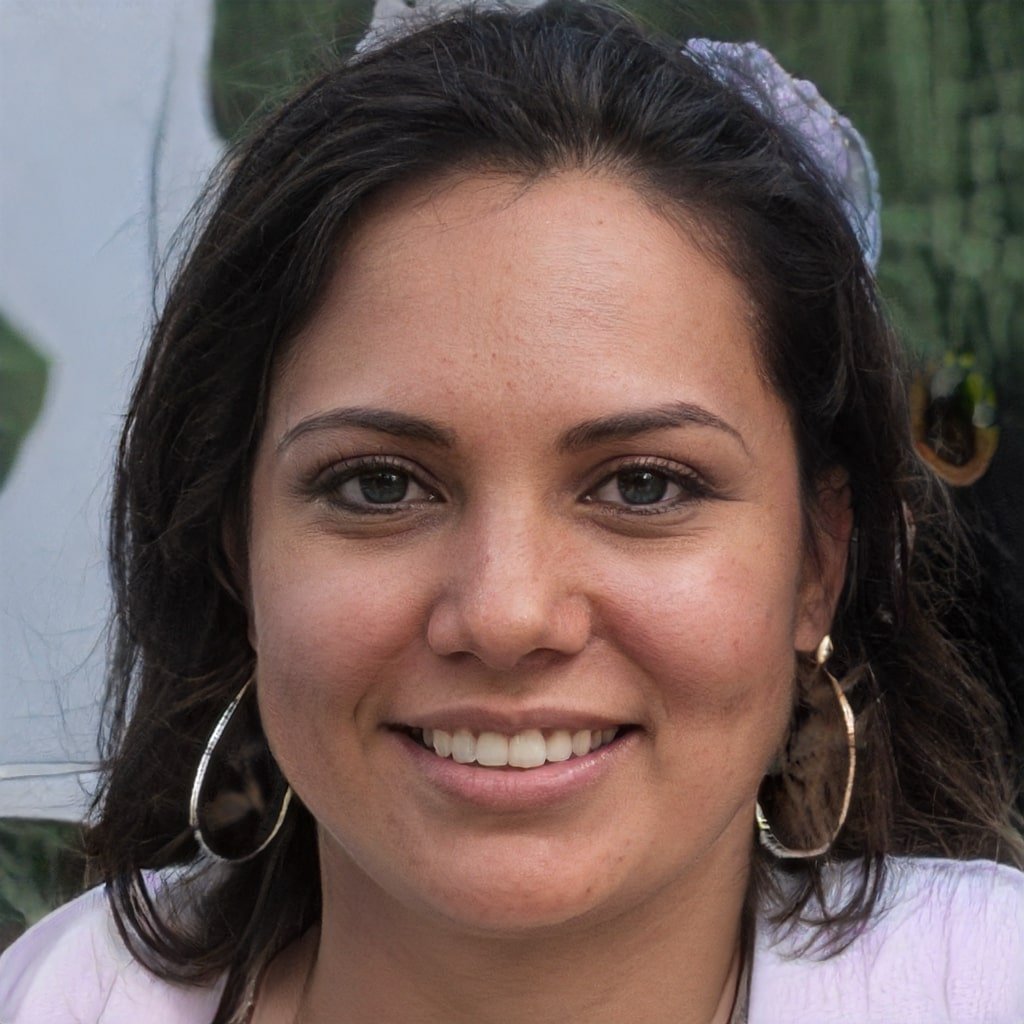